6月 16, 2025
贯穿整个电力电子价值链的全面测试
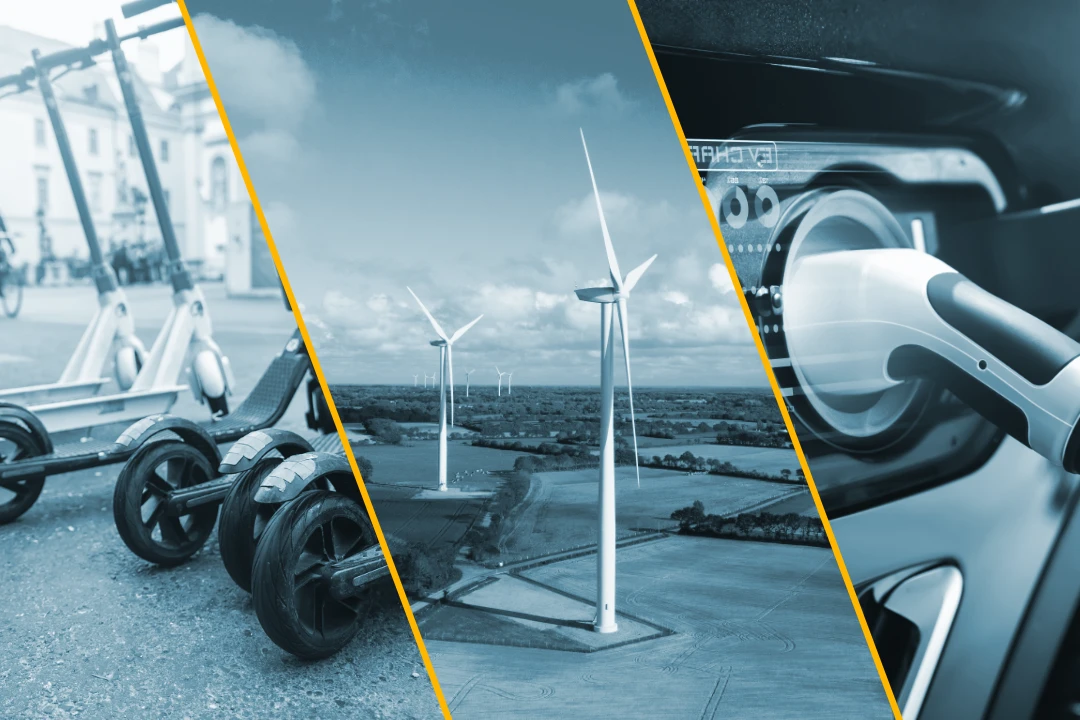
全球电气化进程正加速推进,从先进的电动汽车到可靠的再生能源基础设施,再到高效的工业驱动系统,对电力电子器件提出了极高的要求。这些器件——无论是分立元件、复杂功率模块还是集成电源板——都是现代电力管理的基石。其性能直接决定了系统效率、可靠性与安全性。因此,严格的多层级测试绝非简单的质量控制环节,而是遍布整个制造流程的不可妥协的必要环节。
为何测试?电力电子设备测试的必要性
在电力电子领域,高压和大电流司空见惯,而散热问题往往至关重要,此时即便细微的缺陷也可能引发灾难性故障,导致重大经济损失、安全隐患以及声誉损害。全面测试可确保:
- 长期可靠性:预测并保障电力电子器件在指定负载和环境条件下长期运行的稳定性,确保其全生命周期内的功能完整性。
- 安全保障:识别并消除可能导致电力电子系统危险故障的潜在失效机制,防范人身与财产风险。
- 性能验证:在器件性能极限边缘,持续验证关键电气参数(如开关频率、耐压值)和热特性(如结温、热阻)是否严格符合设计规范。
- 能效优化:通过最小化开关损耗与导通损耗(电力电子系统的核心能效指标),直接降低系统能耗与散热需求,提升整体运行效率。
- 成本控制:在晶圆级等早期生产阶段检测缺陷,避免不合格组件流入高价值装配流程,显著降低因后期失效导致的返工与召回成本。
深度解析:电力电子全生命周期测试策略
电力电子系统的复杂性,要求在生产全流程的每个环节部署针对性的测试方案与专用设备。
1、晶圆级测试:完整晶圆上的初步筛选
在电力电子器件的制造起点——硅晶圆阶段,晶圆级测试便扮演着至关重要的角色。其核心目标是在进一步加工前,精准识别并隔离存在缺陷的芯片(Die)。这一过程需借助高精度的电气探针与专业测试设备,对晶圆上的单个功率半导体芯片进行全面表征。针对功率MOSFET、IGBT及二极管等核心器件,晶圆级测试聚焦于以下关键参数:
- VGE(th) 栅极-发射极阈值电压(模式1和模式2):这是控制器件导通行为的关键参数,需强调其在不同工作模式下的重要性。
- IGES 栅极漏电流:反映栅极氧化层的完整性,翻译需体现其对器件可靠性的影响。
- VBR / ICES 集电极截止电流:验证IGBT和BJT的击穿电压和关断漏电流,需明确其在器件保护中的作用。
- VCE(sat) 集电极-发射极饱和电压:对IGBT的导通损耗至关重要,翻译需突出其对能效的影响。
- VF 耗尽/增强型正向电压:描述集成二极管或特定器件结构的正向电压特性,需区分不同器件类型。
- NTC / 温度传感器电阻:针对集成温度传感元件,翻译需体现其在热管理中的应用。
- UIS / UIL 雪崩:验证器件在雪崩击穿时的能量耗散能力,需解释测试目的。
- dRDS(on) 动态漏源导通电阻:测量动态条件下的导通电阻,翻译需强调其与静态测试的区别。
- Cres, Ciss, Coss, Rgate 寄生电容和电阻:对理解开关性能和栅极驱动要求至关重要,需明确其对器件动态行为的影响。
先进晶圆探针测试方案需具备在微小接触焊盘上进行高压/大电流测量的能力,同时确保测量精度与测试吞吐量。通过这种初步筛选,可在电力电子器件的划片工艺前优化良率。
2、已知良好芯片(KGD)测试:确保划片后裸片质量
在晶圆切割工艺完成后,原本完整的晶圆被分割为独立的单颗芯片(Singulated Die)。此时,针对这些裸硅芯片的已知良好芯片(KGD)测试随即展开。这一环节对采用先进封装技术的产品具有决定性意义,例如系统级封装(SiP)、多芯片模块(MCM)或三维堆叠(3D Stacking)等。这类技术需将多颗芯片集成于单一封装体内,形成高度复杂且成本高昂的器件(尤其在高功率密度电力电子领域,单个封装价值可达数千美元)。若在封装流程中混入一颗存在缺陷的裸片,将导致整颗昂贵器件的报废,造成难以承受的经济损失。
在单颗芯片进入封装流程前,KGD测试旨在通过更严苛的检测手段,全面验证其功能与可靠性。这一环节通常涵盖以下关键技术维度:
- 关键参数复测:重新核验晶圆级测试中已确认的电性指标(如阈值电压、导通电阻),重点检测划片工艺(Dicing)可能引发的机械损伤或静电放电(ESD)失效。
- 增强型电气测试:开展晶圆级无法实施的动态测试(如开关速度测试、短路耐受测试)及功能验证(如模拟实际工况的驱动逻辑测试),尤其针对功率器件需进行雪崩能量(EAS)和米勒平台电压(VGS(th))的严苛考核。
- 光学缺陷筛查:采用高分辨率显微镜或红外检测技术,识别划片后可能暴露的微观缺陷(如硅片微裂纹、金属层剥离),此类缺陷在晶圆级测试中因探针卡接触压力可能被暂时掩盖。
KGD 测试的挑战在于如何精确处理易碎裸片,在不造成损坏的情况下建立可靠的电接触,并执行完整的电气测试,同时保持高吞吐量。最终目标是确保进入后续封装工艺的每个裸片都确实是“已知良好”的。
3、分立功率器件和模块测试
一旦单个芯片被封装或组装成复杂的功率模块(例如,IGBT 模块、SiC 功率模块),测试就会转向验证集成组件或系统的性能。此阶段需要在实际工作条件下进行静态和动态特性测试。
- 静态参数验证:重新测量击穿电压(BV)、漏电流、导通电阻(RDS(on))、集电极-发射极饱和电压(VCE(sat))等参数,以确认封装完整性及功率器件的稳定性能。
- 动态参数表征:这是功率电子领域最具挑战性和关键性的环节,涉及以下精确测量:
o 开关时间(ton, toff, trise, tfall):决定开关损耗和高频性能的核心指标。
o 开关能量(Eon, Eoff, Erec):直接量化器件换流过程中的功率损耗。
o 栅极电荷(QG, QGS, QGD):对栅极驱动电路设计和开关速度优化至关重要。
o 反向恢复特性(IRR, QRR):针对集成或外置功率二极管,影响开关损耗和电磁干扰(EMI)。
o 短路(SC)耐受能力:对IGBT等功率器件至关重要,验证器件从短路状态安全关断的能力,是功率电子系统的关键保护机制。 - 绝缘测试:评估器件承受高压而不发生电击穿的能力,验证高压组件与散热器或底盘之间的绝缘性能。
此类测试通常需要高功率脉冲源、高速测量仪表以及专用夹具和接触单元,以处理大电流/高电压并确保信号完整性。
4、功率电子板测试
测试的最终阶段涉及完整的功率电子板,其中功率模块和分立器件与控制电路、磁性元件及无源元件集成在一起。此阶段的重点在于验证整体系统功能与稳健运行。功率电子板测试对制造商提出了独特挑战:
- 多元技术集成:功率板集成了多种元件,从高压大功率开关和磁性元件到敏感的控制集成电路及通信接口。测试设备需兼容此类多样性。
- 高功率需求:测试通常需要提供高电压(最高3000V)和高电流(最高3000A),以模拟真实工况,且需精确同步与负载控制,这对功率电子至关重要。
- 复杂功能验证:除基础连通性外,功能测试还需验证精密控制回路、功率转换效率、负载条件下的热管理以及功率电子板的故障保护机制。
- 安全要求:测试过程中处理高功率需配备完善的安全协议,并在测试系统中集成安全功能,以保护操作人员和测试设备。
- 大批量生产需求:测试解决方案需具备高吞吐量和并行测试能力,以满足功率电子制造商严苛的生产周期要求。
典型测试方法包括:
- 在线测试(ICT):验证元件放置正确性、焊接完整性及走线导通性,通常涵盖无源元件测量。
- 功能测试(FCT):最全面的测试环节,通过模拟功率电子板的真实运行场景,施加输入电源、控制信号及变化负载,以验证:
o 电压与电流调节精度
o 全工况范围内的转换效率
o 控制环路稳定性及响应时间
o 负载条件下的热管理效能
o 保护电路功能(如过流、过压、过温保护)
o 通信接口完整性(如CAN、以太网) - 高压/大电流功能测试:针对工业与汽车应用,通过实际或模拟高功率条件对板卡进行压力测试,以验证元件可靠性并识别功率电子系统中的潜在缺陷。
SPEA的专业能力赋能功率电子测试的质量与可靠性
为了应对整个电力电子价值链的复杂性和技术需求,高度专业化的自动测试设备 (ATE) 必不可少。从晶圆的超低漏电测量到 IGBT 的大电流动态特性分析,再到复杂电源板的全面功能测试,测试系统必须提供无与伦比的精度、功率处理能力和灵活性。
凭借50年在自动测试设备领域的深厚积淀,SPEA已成为全球功率电子行业综合测试解决方案的领军企业。其测试平台专门针对功率器件制造全流程的严苛要求而设计,覆盖以下关键环节:
功率电子晶圆级与KGD测试:
SPEA提供具备高压大电流能力的先进测试、搬运及探针解决方案,可对晶圆级功率器件及单颗已知合格芯片(KGD)进行精准特性分析。配套的裸晶专用搬运系统可确保即使针对最小巧精密的元件,也能实现稳定接触与精确测量。针对需要双面同步探测或开尔文探测的功率器件,SPEA开发了专用双面晶圆测试设备。
功率电子分立器件与模块测试:
针对封装器件及功率模块(包括IGBT和碳化硅器件),SPEA提供可执行静态与动态特性分析的高端测试系统。这些系统擅长在真实工况下进行关键开关参数分析、高功率循环测试、热性能评估及短路耐受能力验证。
先进功率电子板级测试解决方案:
SPEA的功率板测试系统专为复杂功率电子组件的全面验证而设计。其在线测试(ICT)针床与飞针测试仪集成高压电源(最高3000V/3000A)、精密测量仪器及模块化架构,可执行多样化测试。针对功率板测试的特殊挑战,SPEA解决方案配备强化型传送系统,可处理最大15公斤的大型重型电路板,并采用先进飞针技术精准探测最高150毫米的超高元件。此外,SPEA测试设备通过将光学检测、嵌入式软件烧录及实时时钟(RTC)校准等功能集成于同一测试平台,显著提升生产效率。其并行测试能力在确保大批量生产质量的同时,实现高吞吐量交付。
通过利用尖端技术和深厚的应用专业知识,SPEA助力制造商在电力电子产品的整个生产周期中实现卓越的质量、可靠性和成本效益。与SPEA合作意味着确保为电气化未来提供动力的设备坚固耐用、安全可靠,且性能表现完全符合设计要求。