7月 09, 2025
现代晶圆测试:飞针技术如何降低测试成本与时间
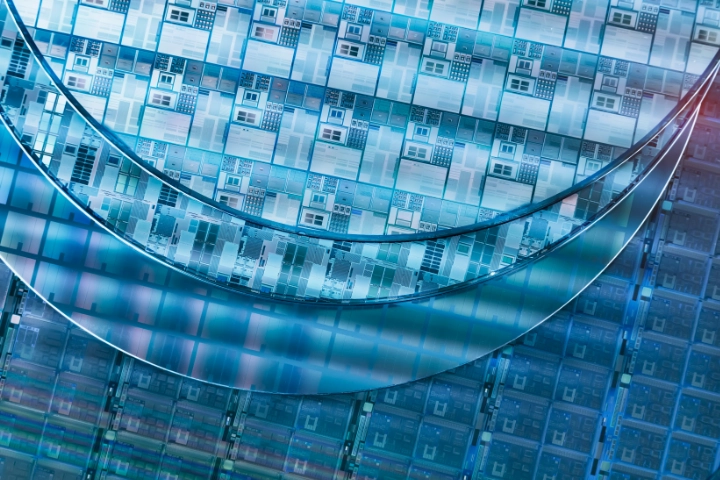
半导体器件向更小、更强大且多功能的方向快速演进,对晶圆测试流程提出了前所未有的要求。随着先进架构和新材料重新定义芯片布局与功能,传统晶圆测试方法已难以跟上发展步伐。飞针测试技术的发展为晶圆探针测试带来了重大转变,针对复杂测试需求提供适应性强且高效的解决方案,同时致力于降低单个芯片的测试成本。
本文将深入探讨影响晶圆测试的最新趋势,并解析飞针测试技术如何彻底改变半导体制造中的这一关键阶段。
现代晶圆测试面临的挑战
晶圆测试变化的主要驱动因素包括:市场对高性能器件需求的激增以及追求最大化产出的同时最小化物理空间。传统晶圆测试方法需将晶圆放置在测试载台上,并通过固定式探针卡接触晶圆表面的测试点。这种方式虽适用于标准的芯片设计,但在面对非标准晶圆布局、多项目晶圆(MPW)及双面芯片时则显得力不从心。此外,半导体行业向更小制程节点和三维(3D)集成技术的转型,进一步增加了测试复杂度,导致成本和测试时间的上升。
当前晶圆测试面临的关键挑战:
- 非标准芯片几何形状
传统矩形芯片正逐渐被非常规形状(如L形、梯形、长条形)取代,以最大化晶圆表面利用率并实现更高效的布局。这些新型设计常导致不对称或镜像化的几何结构,与标准探针卡无法兼容,大幅增加了探针接触的难度。 - 多项目晶圆(MPW)
MPW在原型验证或小批量生产中尤为常见,其通过将不同设计的芯片整合到单一晶圆上以降低成本。然而,由于芯片尺寸、形状及测试焊盘位置的差异,统一测试的难度显著增加。 - 双面及多层芯片
随着三维封装技术的普及,芯片焊盘逐渐从单面扩展至双面,或采用多层设计以实现垂直集成。传统单面探针测试方法难以满足需求,往往需要多次插入晶圆或定制专用设备。
上述复杂性不仅挑战了现有测试方法,还推高了测试时间与成本。为此,行业开发出飞针测试技术,旨在通过高度适应性设计,解决非标准晶圆布局及多维结构的测试难题。
什么是飞针测试技术?
飞针测试技术标志着从固定式探针卡向高度移动探针单元的转变,这些探针单元可独立在晶圆表面移动。与传统晶圆探针台(晶圆在固定探针卡下方移动)不同,飞针测试系统采用多个安装在机械臂上的小型探针卡,使每个探针能够在晶圆表面进行三维(X、Y、Z轴)运动。这种灵活性直接源于飞针技术在印刷电路板组装(PCBA)测试中数十年来的应用演变。
在PCBA测试中,飞针测试作为插件测试(ICT)床针夹具的替代方案而普及。ICT夹具需为每块特定电路板布局定制,重新配置成本高且耗时。而飞针测试可通过编程导航并接触不同测试点,无需固定位置的针床,提供了无与伦比的灵活性,尤其适用于频繁变更布局的中小批量测试或原型验证。其高精度、可调节探针角度与压力的特性,还能在不损伤细间距元件或焊盘的情况下完成精密探测,特别适用于高密度组装。
如今,这种灵活的测试技术被引入晶圆测试领域。飞针测试系统可轻松适应复杂的芯片布局和独特的晶圆配置,使其在多项目晶圆(MPW)、非标准芯片几何形状及双面设计中极具价值。通过借鉴PCBA测试中验证过的灵活性,飞针技术成为满足现代晶圆测试需求的强大工具,并且以下几方面优势显著:
- 更高并行度:多个探针可同时在晶圆不同区域工作,显著提升吞吐量。
- 增强灵活性:每个探针可独立对准特定芯片,适用于复杂非均匀晶圆布局。
- 双面测试:通过晶圆上下方的探针,飞针技术可一次性完成双面芯片测试,并支持贯通芯片两侧的连通性检测。
飞针测试技术如何提升晶圆测试效率
飞针测试技术能够通过创新方法应对现代晶圆测试的复杂性:
1.多项目晶圆的单次插入测试
传统测试中,多项目晶圆内的每个独特芯片布局都需要单独的探针卡或多次探针台插入才能完成全片测试。而飞针技术可将每个探针臂分配至晶圆中特定的芯片或测试模式。例如,一个探针臂可配置为测试长条形芯片,另一个则处理L形芯片。这减少了探针卡更换需求,并显著降低了插入与校准时间,从而简化了测试流程。
2.适用于双面晶圆的双面探测技术
双面晶圆(硅基板两侧均有暴露焊盘)的测试面临显著挑战。传统探针台需分别对晶圆两侧进行独立插入测试,每次插入均需重新校准对齐。而独立上下布局的飞针可同时接触晶圆两侧,实现以下功能:
- 连续性测试:通过同步检测双面焊盘连接,飞针测试系统支持贯通芯片验证及高级电气测试。
- 多层晶圆测试:微机电系统(MEMS)等复杂器件常需多层测试以验证机械与电气功能。飞针通过精准对齐并接触各层或暴露焊盘,简化了这一流程。
3.非标准芯片几何形状的优化
许多现代晶圆设计通过采用非传统芯片形状来最大化表面积,这可能导致晶圆上出现不对称或镜像布局。飞针技术通过允许每个探针卡针对特定几何形状进行定制,解决了这一挑战。这种灵活性将测试能力扩展到非标准几何形状,且无需额外探针卡配置。例如:
- 可定制探针卡布局:每个探针卡可独立配置,更易于测试不规则芯片形状。
- 镜像与旋转布局适配:探针可独立调整以适应每个芯片的方位,简化了高密度器件中常见的镜像或旋转布局的测试流程。
4.自动翘曲补偿和探针标记检测
随着晶圆厚度减小且结构日益复杂,因应力或加工工艺导致的翘曲(弯曲变形)问题愈发显著,直接影响探针对齐精度。飞针系统可集成先进的激光表面测绘技术,通过评估晶圆平整度并自动调整每个探针的位置,以匹配晶圆的实际曲率。这种补偿机制确保了精确接触,最大限度减少探针与焊盘的错位风险,同时降低对晶圆的损伤概率。
此外,高分辨率光学检测系统显著提升了探针标记检测能力。通过在探针接触前后捕捉图像,系统可验证接触点状态,帮助工程师实时监控并优化每个探针的接触精度。激光测绘与光学检测的结合,构建了一套强大的自动化解决方案,即使在翘曲晶圆上也能稳定维持探针对齐精度。
飞针测试在晶圆测试中的应用及意义
基于飞针架构的晶圆探测器广泛应用于消费电子、汽车、医疗设备等多个领域。其处理复杂晶圆设计、高密度芯片及非常规芯片形状的能力,为诸多领域的进步提供了支持:
- 微型医疗设备:需要高度集成的多功能芯片,常采用双面或多层芯片结构,飞针测试技术可满足其紧凑设计需求。
- 电力电子:如功率晶体管等需要大电流测试的设备,采用飞针测试可提升测试高精度与灵活性。
- MEMS器件:MEMS应用的多层结构可通过飞针直接访问并测试各层,无需重新配置,同时支持电阻、电容等高精度参数测量。
- 汽车与航空航天电子:汽车行业对传感器和控制单元的可靠性要求极高,且这些产品通常为小批量定制化生产。飞针测试系统支持高效的多项目晶圆(MPW)测试,完美适配此类需求。
- 先进消费电子:微型化设备(如可穿戴设备和物联网终端)需密集封装,并常涉及双面或多层设计。飞针可在保证速度与精度的前提下,完成连续性测试及分层验证。
飞针技术赋能测试效率加速上市时间
飞针测试技术最具吸引力的特点之一,是其降低半导体器件测试成本并加速产品上市的能力。通过减少多次插入测试的需求及探针卡更换频率,飞针技术简化了晶圆级测试流程。这直接缩短了生产周期,使得在更短时间内测试更多晶圆成为可能。
此外,飞针测试能以最小调整适应新设备配置,使测试流程具备“面向未来”的特性,可从容应对晶圆设计的进一步创新。对于制造商而言,其影响体现在两方面:测试流程能紧跟快速的设计变更,同时通过减少对定制探针卡的需求及劳动密集型重新配置工作,有效控制成本。
结论
飞针测试技术正以前所未有的灵活性、精度与适应性,重塑晶圆测试的格局。随着半导体行业持续创新,推出更复杂、紧凑且多功能的器件,飞针技术提供了能够满足新型芯片架构与非标准晶圆布局测试需求的多功能解决方案。
对于开发先进半导体器件的企业而言,飞针测试技术对优化测试流程、降低总成本及加速从晶圆到终端产品的转化提供了路径。该技术不仅解决了当下的测试挑战,还为芯片设计演进背景下的未来测试创新奠定了基础。
飞针测试技术远不止于一种新工具——它标志着半导体测试方式的范式转变,使行业得以突破器件设计与性能的边界。